DIN and ANSI standards have clear requirements for the connection methods of UPVC and CPVC pipe fittings, which are designed to ensure the sealing, stability and long-term reliability of the pipe fittings after installation. The following are the specific requirements for the connection methods of UPVC and CPVC pipe fittings according to these two standards:
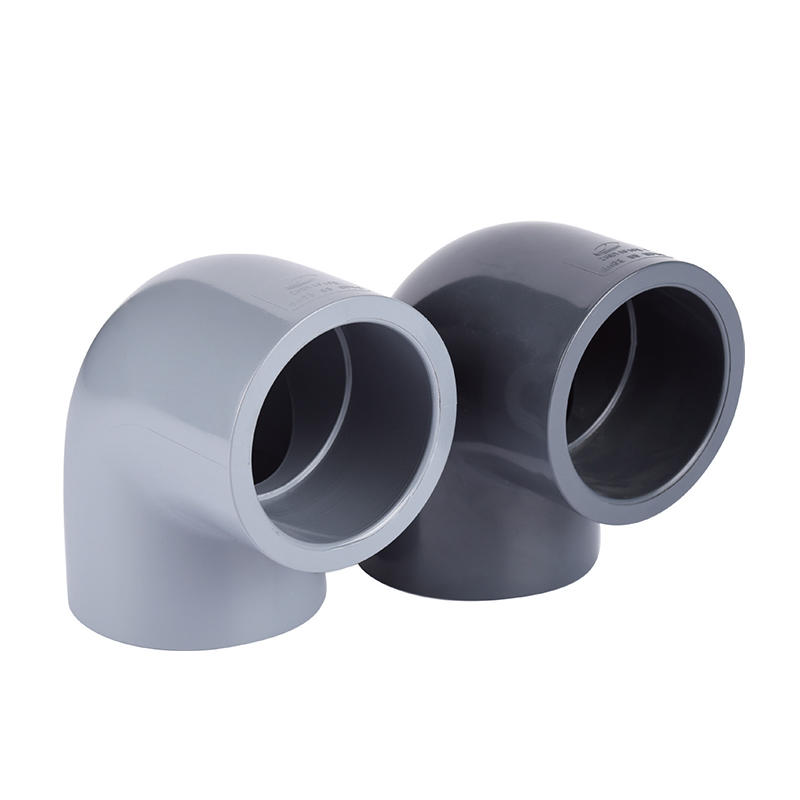
UPVC/CPVC 90° Elbow
1. Types of connection methods
Whether it is DIN or ANSI standards, the commonly used connection methods of UPVC and CPVC pipe fittings mainly include the following:
Socket Connection: By inserting the pipe into the socket of the pipe fitting and sealing it with adhesive or sealant.
Threaded Connection: Connecting pipe fittings and pipes by thread, usually used in smaller diameter systems.
Flanged Connection: Connecting pipe fittings to pipes by flanges and bolts, suitable for occasions that require frequent disassembly or high-pressure systems.
Butt Welding: Connecting pipe fittings to pipes by hot melt welding, suitable for large diameters or occasions requiring high-strength connections.
2. DIN standard requirements for connection methods
Socket connection:
Adhesive requirements: Special adhesives that meet DIN standards must be used to ensure bonding strength and sealing.
Insertion depth: The depth of the pipe inserted into the socket of the pipe fitting should meet the minimum and maximum values specified in the DIN standard to ensure the stability of the connection.
Sealing test: A sealing test is required after the connection is completed to ensure no leakage.
Threaded connection:
Thread specifications: The threads must meet standards such as DIN 2999 or DIN 259 to ensure the accuracy and compatibility of the threads.
Sealing materials: Raw tape or sealant is usually required to ensure the sealing of threaded connections.
Flange connection:
Flange standards: Flanges must meet standards such as DIN 2501 or DIN 2515, including flange size, pressure rating and sealing surface form.
Bolt requirements: The material and specifications of bolts and nuts should meet DIN standards to ensure the strength and reliability of the connection.
Welding connection:
Welding process: Welding must meet DIN 1988-200 standards, including welding equipment, welding parameters and welding quality control.
Welding quality inspection: After welding is completed, visual inspection and non-destructive testing are required to ensure that the welding quality meets the requirements.
3. ANSI standard requirements for connection methods
Socket connection:
Adhesive requirements: Adhesives that meet ANSI/NSF 14 standards must be used to ensure bonding strength and chemical compatibility.
Insertion depth: The insertion depth should meet the range specified by the ANSI standard to ensure the stability and sealing of the connection.
Sealing test: After the connection is completed, a pressure test is required to ensure no leakage.
Threaded connection:
Thread specifications: The threads must meet the ANSI B1.20.1 standard to ensure the accuracy and compatibility of the threads.
Sealing material: Raw tape or sealant is usually required to ensure the sealing of threaded connections.
Flange connection:
Flange standards: The flange must meet the ANSI B16.5 or ANSI B16.47 standards, including the flange size, pressure rating and sealing surface form.
Bolt requirements: The material and specifications of the bolts and nuts should meet the ANSI standard to ensure the strength and reliability of the connection.
Welding connection:
Welding process: Welding must comply with ANSI/AWWA C605 or ANSI/AWWA C600 standards, including welding equipment, welding parameters and welding quality control.
Welding quality inspection: After welding is completed, visual inspection and non-destructive testing are required to ensure that the welding quality meets the requirements.
4. Commonalities and differences
Commonalities:
Sealing requirements: Both DIN and ANSI standards have strict requirements on the sealing of the connection to ensure no leakage under the design pressure.
Material compatibility: Both standards emphasize the chemical compatibility of adhesives, sealing materials and welding materials to prevent material aging or corrosion.
Differences:
Standard details: DIN standards focus more on the technical specifications of the European market, while ANSI standards are more in line with the technical requirements of the North American market. For example, the thread specifications, flange sizes and pressure levels are divided differently.
Test methods: DIN and ANSI standards may have slight differences in test methods and acceptance criteria, such as the pressure range and duration of the sealing test.
5. Practical application suggestions
Choose a suitable connection method: Choose a suitable connection method according to the pressure, temperature, medium and installation environment of the system. For example, socket connections are suitable for medium and low pressure systems, and flange connections are suitable for high pressure or systems that require frequent disassembly.
Follow standard requirements: During installation, strictly follow the requirements of DIN or ANSI standards to ensure the quality and reliability of the connection.
Quality control: When purchasing pipe fittings and connection materials, choose products that meet the standards, and perform necessary tests after installation, such as pressure tests or sealing tests.